From the idea to the finished tool
The cooperation between Mikron Tool and the customer often starts long before the purchase of a tool, before the processing cycle is determined, or before the tools are defined.
The challenging part begins when the customer presents a workpiece which he would like to machine economically on his equipment.
Use the know-how of the specialists
Every sales engineer at Mikron Tool understands the requirements of the customers. He is able to prepare offers, define tools, use them in the machine and thereby determine the optimal cutting parameters. He knows carbides and coatings, tool geometries and chips, he has experience with a great variety of materials to be machined.
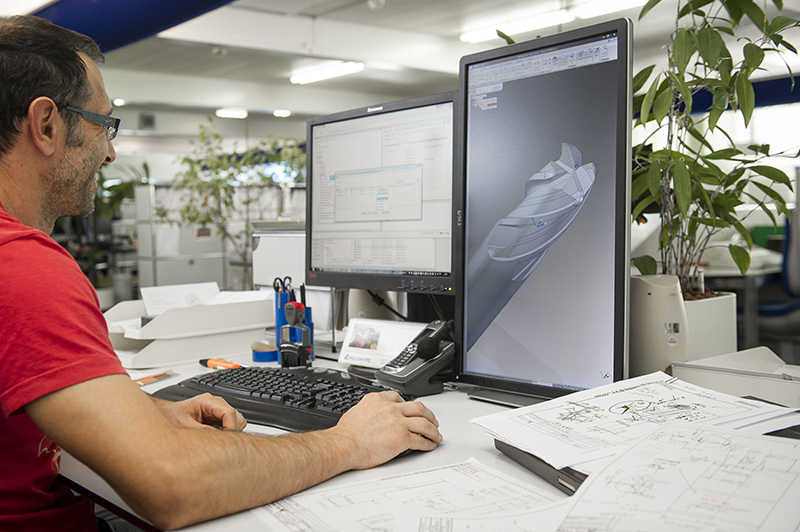
Even when the customer approaches the specialists with already clear ideas and a tool drawing and "only" wants a corresponding offer, it is necessary to clarify the exact requirements. What tolerance is to be maintained, what material will be processed, what cycle times are calculated? The selection of the tungsten carbide depends on that, the coating and maybe the geometry could be further optimized.
It becomes more complex when the working cycle for a workpiece as well as the right tools have to be defined. Is a standardized tool adequate or can a combination tool be used more profitably in this case? Which is the ideal process for the machining of a workpiece on a CNC milling machine, linear or rotary transfer machine or automatic lathe? The tool specialist of Mikron Tool is often confronted with this question at the first contact with a customer.
Customer projects: Higher performance through testing
Testing new tungsten carbide drills, before they are purchased or used in serial production, redefining the parameters in order to reduce cycle times, improving or redefining processes or even finding the adequate tool for new materials? Rarely does a manufacturing plant have free capacity on its machines to perform the necessary tool tests. For these cases, Mikron Tool has developed a service offering: CrazyService Products. A competent team of tool specialists, machining engineers and programmers is available to the customer at the Technology Center.
This team uses practical tests to determine the ideal tool, the optimal process or the best strategy for the customer's application, always based on his specific needs and conditions. Five packages represent different service levels. Everything is possible: from a simple tool test before buying a CrazyTool, to the definition of parameters with CAM programming, to tool life tests in order to calculate the cost/part, and up to complete solutions for producing a new part. What is delivered here is not tools, but know-how and test reports with the results achieved. Depending on the project, this may include a tool evaluation and recommendation, information on the ideal parameters, CAM programming, and if requested, measurement protocols and videos. All this serves the goal of supporting the customer in the production optimization or offering new solutions for the processing of challenging workpieces.
Competence in the service of the machine manufacturer
Mikron Tool has been working successfully for years with many machine manufacturers. Our engineers can make a valuable contribution, both with their engineering expertise and with high-quality standardized tools, by being involved in project development right from the bidding stage of a machine.